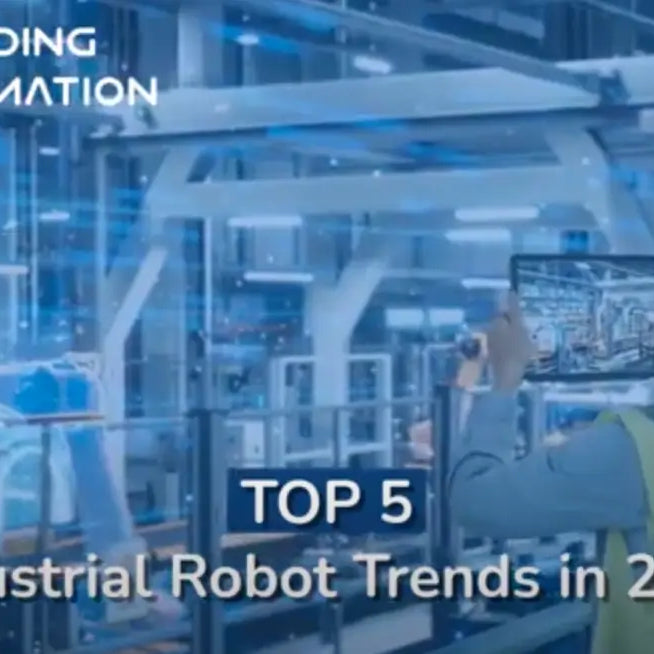
Orders & Worldwide
Orders & Worldwide
A Robotic Servo Drive is an Electric Motor coupled with integrated sensors & or hardware which senses any type of Mechanical Error, Fault or Malfunction and thus during sure that Electric motor working position, speed & power matches as desired by the Controller & or PLC. The Robot Servo Drive are known for its Precious Working & robust performance. That’s why this Specialized Motor Mechanism/Configuration has widely spread in Industrial Robots assisted Manufacturing.
Robot servo drives are numerous & varied- form small and cheap motor servo drives, mini or Nano & or pico drives, as well as robotic Heavy Torque industrial models for heavy-duty industrial tasks.
2: What is A Robotic Servo Drive Mechanism ???
A Basic Robot servo drive mechanism comprises of the following parts:
A Robot Controller Box or PLC that detects input signals & then interprets them into required motion parameters
A specialized motor which is normally a small high speed DC motor linked to the Robotic Controller or & PLC by an H-bridge Circuit configuration.
A Gear-head that reduces the Servo Motor RPM’s while gradually increasing torque as required.
A Robotic Precision Sensor that always know the exact position of the Servo Drive output shaft.
3: The Different Kinds Of Robot Servo Drives
Depending on the Sensor Signal processed by a Controller or PLC, a robot servo drive works. Also it’s worthy to note about types of signals mechanisms i.e., Analog Signal & Digital Signal Mechanism’s. Likewise we have two types of signals Analog Signal & Digital Signal as they are similar both on the outside and the inside of working configuration. The major difference is the working principle.
Analog motor servos use on/off pulses of voltage. The longer a pulse is the fast a motor rotates and the more torque it creates as signal is only on when you command a task, these devices are energy-efficient. Due to this reason their response is quite slower as compared to digital servo drives. On average, on/off frequency is roundabout 50 pulses per second. Analog servo drive mechanisms cannot be programmed.
But on the other side a Robotic Digital Servo drive provide frequency of about 300 pulses in a second which gives best precision & allows for refined motion adjustment as required. These drives can decelerate & acquire acceleration very fast and as such torque capacity exceeds several times as compared to of analog ones. Also a built-in microprocessor enables us to configure them for lower deadbands & higher peaks of torque.
According to the input current type, Robot Servo Drives are of two kinds i.e., Alternating Current (AC) & Direct Current (DC). DC Servo Drives are well known as they have Low Inductive Reactance that’s why they generate better positioning accuracy & instant response. AC Servo Drives are famous for their High Tolerance & most efficient working bearings.
The AC servo drives class has further classification as under:
The Positional rotation servos drives use mechanisms where the output shaft rotates in a range of roundabout 180 degrees. In Positional rotation servo drives the Gear Mechanism uses mechanical stops thus by preventing movement beyond the limits.
While a Continuous rotation servo drive can turn in both directions i.e., clockwise and anticlockwise directions with variable velocities according to the command signal from the Controller &/or PLC. These servos are mostly used in robotic wheels.
While the Linear servo drives operate likewise a positional rotation servo drive either in the forward or backward directions.
4: Advantages of Robot Servo Drive.
Today, Industrial Robots are very different from Servo Applications in Motion because industrial robots are rapidly evolving to the smartest & newest Technologies. That’s why General mechanisms have been very much modified for industrial robots related tasks.
That’s why smart servo drives have special fittings so that they can be easily incorporated into Robotic limbs.
Possible inputs include time, speed & position.
By employing Serial Communication Mode allows to get different kinds of return i.e., temperature, velocity & lot of other data,
With flexible feedback, a Controller Box &/or PLC can adjust component Statistics & Working on time or can even shut them off in case of a Malfunction.
Multiple Robot Servo Drives can be tasked on a single line without any need to link them directly with the Controller Box &/or a PLC.
Now we can see that the Robotic Modifications have provided biggest accuracy in motion control on the basis of detailed feedback from the Robot. That’s why Easy integration & operation of multi servo motor drives on the same line is now very easy.
5: Role of Controller in Running A Servo Drive.
In Industrial Robotics the Controller Box &/or a PLC are Standalone Modules which are programmable devices & which can be programmed via a Teach Pendant that stores and runs that Computer Program/Software or Set of Instruction Codes which are programmed. Programming is done in a lot of languages i.e., Visual Basic, BASIC, C+/C++, Python & a lot of other compatible languages confirming to Industrial Robotics Specifications.
Industrial robot Controllers & PLC have built-in safety devices to prevent overload or even fully stop a robot in event of any component failure, break or malfunction.
Robot Servo Drives tend to focus on receiving the input commands from the Controller/PLC & thus switching the power transistors off & on. This helps in creating the voltage & current required for generating the essential speed & torque.
With day by day new advances in microprocessors & newest Switching Systems, robot Controllers, PLC’s, Drives are becoming more and more integrated mostly in centralized Industrial Systems where all electronics are located in one control cabinet. But in Decentralized Industrial Systems, the motion controller is within the Control cabinet or PLC while the motor servo drives communicate with the motion controller via a motion control field bus.
3HAC035381-001 | ABB Servo Drive Unit DSQC417 |
3HAC035301-001 | ABB DSQC406 Servo Drive Unit |
3HAC036260-001/04 | ABB DSQC431 Servo Drive Unit |
00-198-268 | KUKA Servo Drive KSP 600-3x40 |
00-122-285 | KUKA KRC2 KSD1-16 Servo Amplifier |
00-198-260 | KUKA Driver KPP 600-20-1X40 |
A06B-6200-H022#H600 | FANUC Servo Drive Amplifier |
A06B-6240-H209 | FANUC Servo Drive Amplifier |
A06B-6220-H022#H600 | FANUC AC Servo Amplifer |
SGDV-330A01A002000 | YASKAWA AC Servo Driver |
SGDR-SDA710A01BY32 | Yaskawa Servo Drive Amplifier |
SGD7S-120A20A | Yaskawa Servo Drive Amplifier |
Leave a comment